結論からいうとリーンスタートアップとは:
無駄を徹底的に排除し、スピード感を持って顧客満足度の高い製品やサービスを開発するマネジメント手法を指します。このアプローチは、特にスタートアップ企業や新規事業開発において、限られたリソースで効率的に市場に適応するために活用されています。
その核心は、最低限の機能を持つ製品やサービス(MVP:Minimum Viable Product)を迅速に市場投入し、顧客からのフィードバックを基に継続的な改善を行う点にあります。
リーンスタートアップの背景と歴史
リーンスタートアップの概念は、アメリカの起業家エリック・リース氏が自身の経験を基に2008年に提唱しました。
彼は、過去の起業経験で顧客のニーズを十分に理解せずに製品開発を進めた結果、失敗を経験しました。この反省から、顧客の声を早期に取り入れ、無駄を省く手法としてリーンスタートアップを体系化しました。
2011年に出版された著書『The Lean Startup』は、世界中の起業家や企業に影響を与え、この手法が広く認知されるきっかけとなりました。
リーンスタートアップは、日本のトヨタ生産方式に由来する「リーン生産方式」の思想を取り入れています。
トヨタ生産方式は、製造プロセスにおける無駄を徹底的に排除し、効率的な生産を追求する手法として知られています。この考え方をビジネス開発に応用し、最小限のリソースで市場のニーズに適応する方法論として進化しました。
リーンスタートアップの3つのサイクル
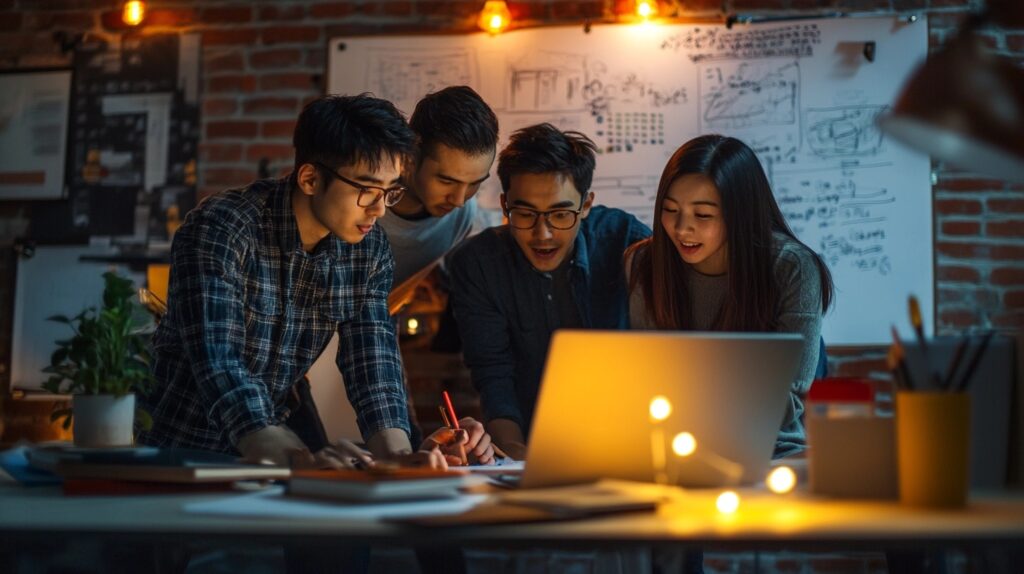
リーンスタートアップは、以下の3つのサイクルを繰り返すことで、効率的な事業開発を実現します。
- 構築(Build):ターゲットとなる顧客のニーズに基づき、製品やサービスのアイデアを具体化します。その後、必要最低限の機能を持つプロトタイプ(MVP)を短期間で開発します。
- 計測(Measure):MVPを実際の顧客に提供し、その反応や使用状況をデータとして収集します。これにより、製品やサービスの市場適合性や改善点を明らかにします。
- 学習(Learn):収集したデータを分析し、仮説の検証や必要な改善を行います。場合によっては、ビジネスモデルや戦略の大幅な転換(ピボット)を検討します。
このサイクルを迅速かつ継続的に回すことで、顧客の真のニーズに応える製品やサービスを効率的に開発することが可能となります。
リーンスタートアップの成功事例
リーンスタートアップの手法は、数多くの成功事例を生み出しています。以下に代表的な企業の事例を紹介します。
Dropbox
オンラインストレージサービスを提供するDropboxは、初期段階で簡単なデモ動画を公開し、ユーザーからのフィードバックを収集しました。これにより、製品の方向性を迅速に修正し、ユーザーのニーズに即したサービスを提供することに成功しました。
Zappos
オンライン靴販売のZapposは、最初に地元の靴店の在庫をオンラインで販売し、需要をテストしました。この実験的アプローチにより、オンラインでの靴販売の可能性を確認し、後の成功につなげました。
これらの企業は、リーンスタートアップの手法を活用し、最小限のリソースで市場の需要を的確に捉え、成功を収めています。
柔軟性とスピードで激しい競争を勝ち抜く
リーンスタートアップは、無駄を省き、迅速に市場のニーズに適応するための効果的な手法です。特に、変化の激しい現代のビジネス環境において、柔軟性とスピードは重要な要素となっています。この手法を理解し、適切に活用することで、ビジネスパーソンは新たな価値を創造し、競争力を高めることができるでしょう。
リーンスタートアップの手法をどのように活用して、皆さんのビジネスに革新をもたらしますか?ぜひ、具体的なアイデアや経験を共有してください。
出典
- Ries, Eric. The Lean Startup: How Today’s Entrepreneurs Use Continuous Innovation to Create Radically Successful Businesses. Crown Business, 2011.
- Blank, Steve. The Startup Owner’s Manual: The Step-by-Step Guide for Building a Great Company. K&S Ranch, 2012.
- Harvard Business Review. “Why the Lean Start-Up Changes Everything.” May 2013. https://hbr.org/2013/05/why-the-lean-start-up-changes-everything
- Toyota Production System. “The Lean Manufacturing Methodology.” https://www.toyota-global.com/company/vision_philosophy/toyota_production_system